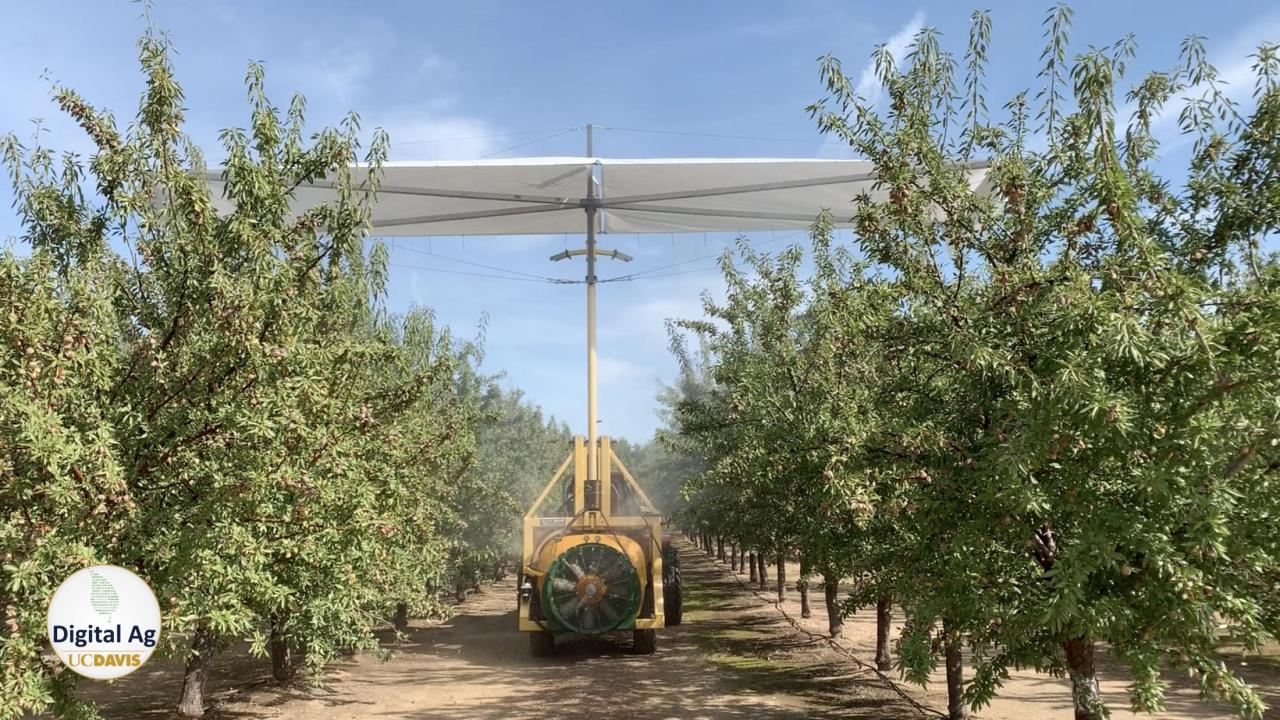
Spray Backstop
Principal Investigator: Alireza Pourreza
Project Sponsor: Almond Board of California
Collaborators: Ali Moghimi, German Zuniga-Ramirez, Bruno Batista da Silva, Franz Niederholzer, Peter Larbi
Published in:
Pourreza, A., Moghimi, A., Niederholzer, F. J., Larbi, P. A., Zuniga-Ramirez, G., Cheung, K. H., & Khorsandi, F. (2020). Spray Backstop: A Method to Reduce Orchard Spray Drift Potential without Limiting the Spray and Air Delivery. Sustainability, 12(21), 8862.
One of the major issues in almond pesticide application is spray drift while assuring good coverage, particularly on treetops. Unmanaged spray drift contributes to environmental contamination, and it may also result in increased regulation for pest control application. Additionally, spray droplets' offside movement causes a significant danger to farmworkers, nearby residential areas, and off-target crop. Therefore, controlling spray drift becomes a high priority for growers.
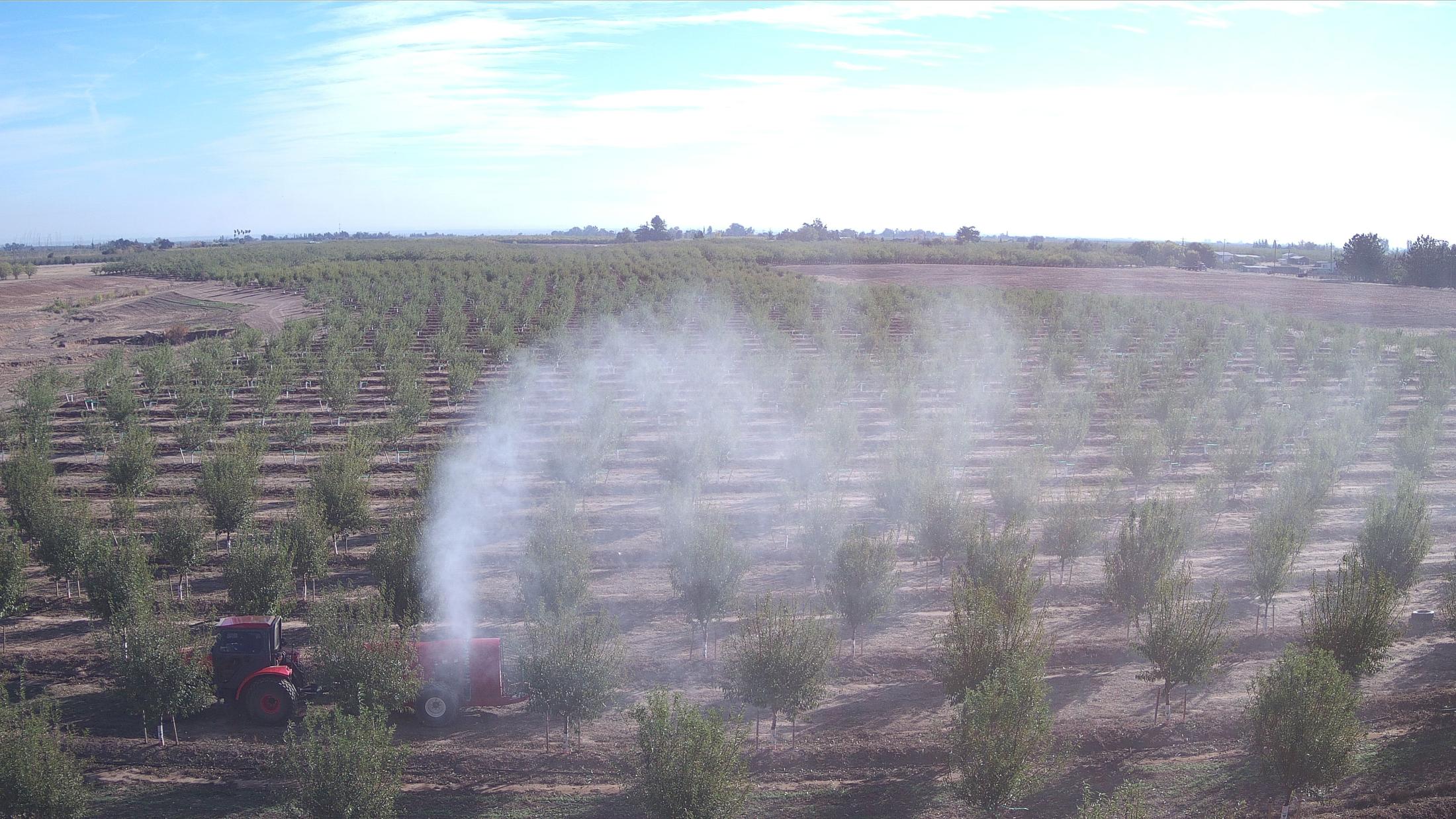
In this project, we designed and fabricated the prototype of a spray backstop system. This system includes a mast and a screen structure covering the trees and blocks the spray droplets escaping from treetops. To evaluate spray drift reduction with the backstop system, we used a mixture of water and Fluorescent dye to spray an almond orchard with and without the spray backstop. A continuous loop ribbon system was used to capture all off-target droplets escaping from the top and sides. Leaf samples were also collected from the treetops located on both sides of the row and from two sides of trees (near and far). Cuts of the ribbon and leaf samples were analyzed in the laboratory to quantify dye deposition. The results showed an overall reduction of 78% in the airborne drift when the backstop system was used compared to spraying with the same setting but without the backstop. Although this prototype was not designed to provide drift reduction from the sides, a fair drift reduction of 47% from sides was observed. The laboratory analysis showed that leaves on treetops received 9% better spray deposition when spray backstop was used. These results clearly proved the effectiveness of spray backstop in reducing airborne drift and improving the treetop coverage.
Achieved Objectives
- The spray cloud movement was determined by monitoring aerial RGB and thermal views of an almond orchard spray operation with a standard-setting.
- The prototype was designed and fabricated for young almond orchards based on how the spray cloud moves from the first objective. The fabrication was conducted at the BAE shop. The prototype was test-assembled in Davis and then transferred to Nickels Soil Lab for on-site test.
- The spray drift reduction and coverage improvement in treetops were quantified by the dye deposition analysis method. A sprayer was filled with a mixture of water and Fluorescent dye and used to spray an almond orchard. Drift evaluation was performed using the continuous loop sampling method with and without the backstop system. The experiments were conducted at the Nickels Soil Lab.
Monitoring spray cloud movement
In October 2018, an unmanned aerial system was used to capture thermal and RGB images and videos of the spray cloud movement from multiple directions to the sprayer.
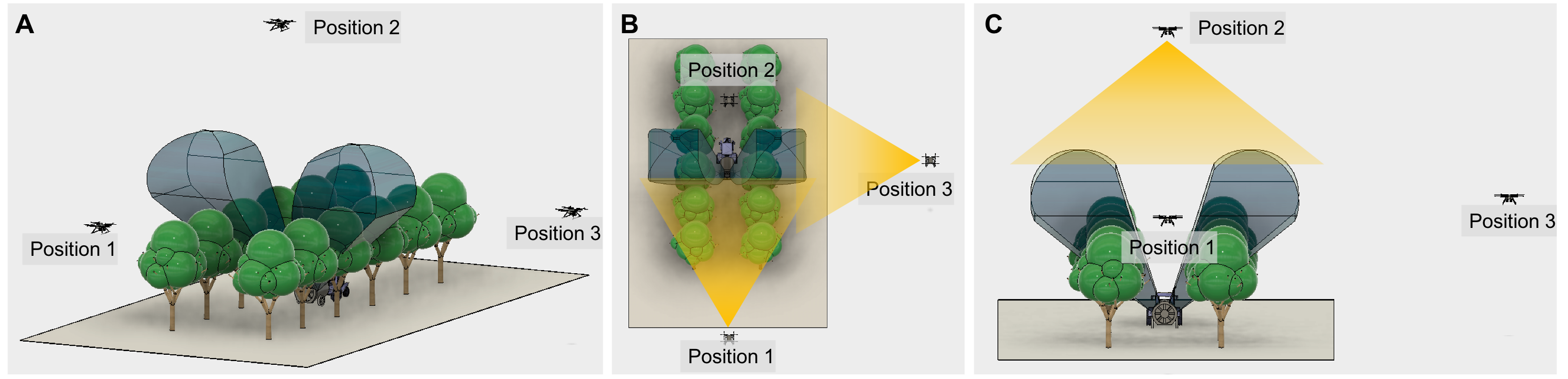
Two types of imagery from 3 different views. The aerial imagery was analyzed, and the pattern of spray cloud movement in a young almond orchard was determined. The results were used to design the structure and size of the prototype of the spray backstop system.
Spray Backstop
The backstop system includes a foldable mast structure powered by the tractor hydraulic system. The height of the backstop was about six meters from the ground at the upright position. To block the spray droplets escaping from trees tops, two waterproof tarps, with 8-millimeter thickness and 12x12 weave, were used for each side of the sprayer. It had grommets located every 18 inches, which were used for tying the tarp to the backstop. The width and total length of the screen was about 2 meter and 10 meters, respectively.
Field experiments
The orchard used for this experiment was planted in 2009 (11th leaf) and located at the Nickels Soil Lab. Rootstock was Lovell peach seedling. The following setup was used for spraying the almond orchard:
- The forward speed of tractor: 2 MPH
- System pressure: 160 psi
- Nozzles: Spray Systems TXR80049VK; 4 nozzles per side; 0.971 GPM/nozzle, 3.88 GPM/side of the sprayer.
Fluorescent dye (Pyranine) was mixed with water in the sprayer tank (approximately 54g of tracer with 130 gallons of water). The backstop system's effectiveness in blocking drift was evaluated by a continuous loop sampling method in which a one-inch cotton ribbon was stretched above the trees and on the rows adjacent to the row that was sprayed with and without the backstop system. The cotton ribbon was cut at 60 cm/piece. The top section had 23 samples, and the side sections (right/left) had 12 samples each. To evaluate the spray backstop's impact on the spray converges, leaf samples were collected from the treetops on both sides of the sprayer. Sampling was done from two sides of each tree: the side near the sprayer and the side farther away from the sprayer. The ribbon and leaves samples were placed in pre-numbered bags, marked with the sample location in the continuous loop, and shipped to the UC Kearney REC to assess fluorescent dye deposition. Samples were analyzed by fluorometry technique at Dr. Peter Larbi’s lab located at Kearney REC, Parlier, CA.
Evaluation with Aerial imaging
For visual assessment of the spray cloud movement, aerial photos/videos were captured during the experiments. A DJI Mavic 2 Pro equipped with a 20MP camera was used for aerial imagery. The figure below shows the aerial images captured during the spraying and how the spray cloud lifted the ribbon from the rest position (compare Figures A and B). Alternatively, the ribbon remained in its rest position (Figure C) while using the backstop since the cloud was captured under the tarp. A comparison between Figure B and C shows how the backstop system effectively blocks the spray droplets that pass treetops and pushing them back to treetops. The dye deposition results validated this observation.
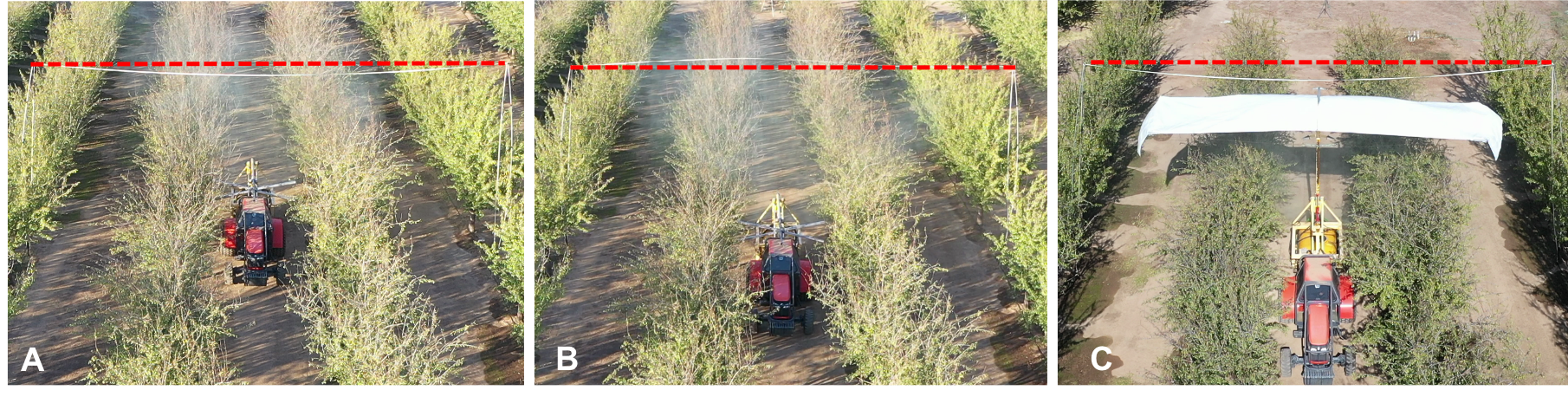
Results
The analysis of dye deposition on the ribbon samples at the top and sides of the sprayer demonstrated a significant reduction in drift potential, largely from the trees' top. The figure below shows the result of the dye deposition on the ribbon. With the backstop system, an average drift reduction of 78% at the top was measured comparing to spraying without the backstop system. Drift potential from the sides is a function of the target canopy size and foliage density. Using the spray backstop system caused an overall side drift reduction of 47%, including a 26% reduction from the left side and a 58% reduction from the right side. The dye deposition pattern on the ribbon indicated more drift from the right and top-right sides that may suggest there was a wind from left to right during the test.
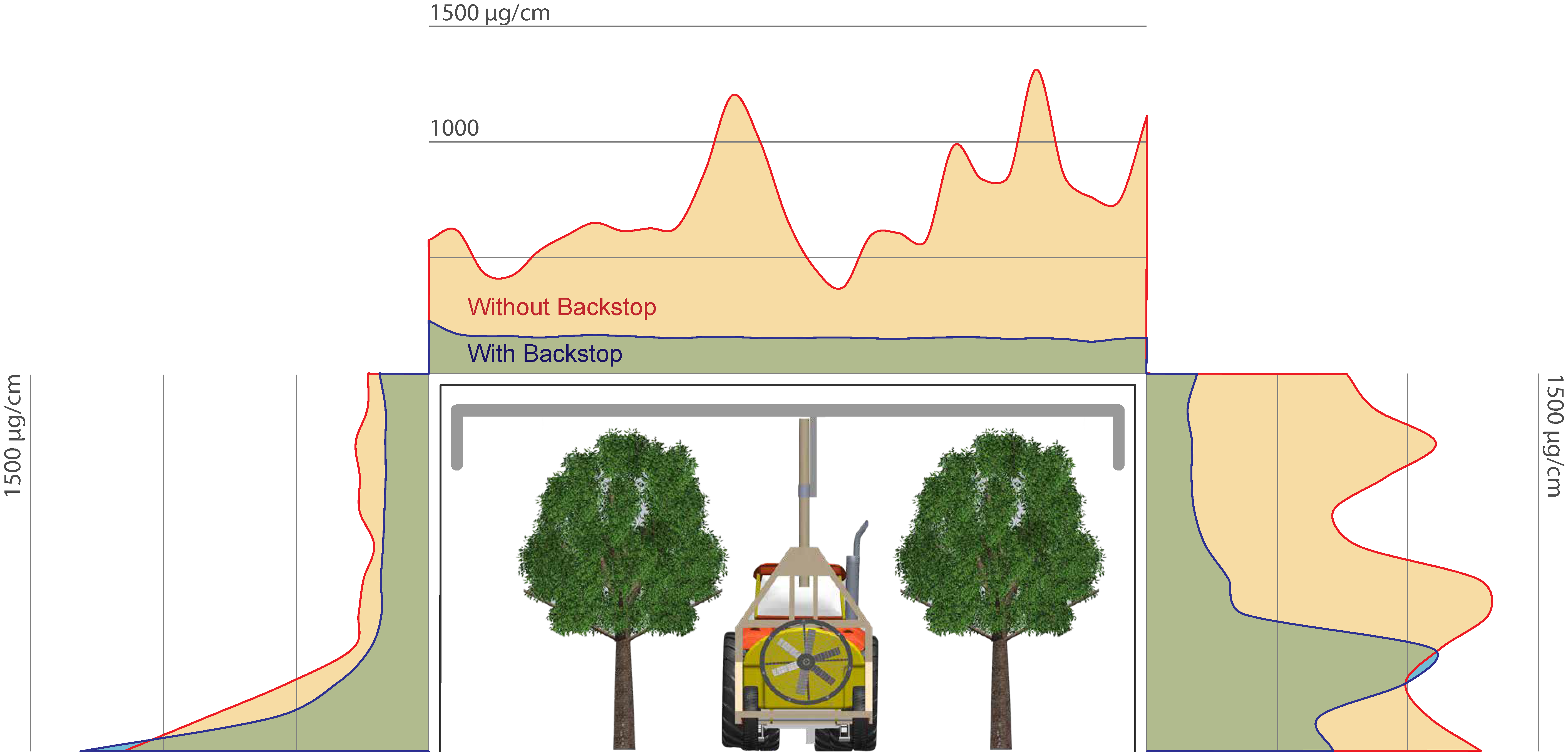
The figure below illustrates dye deposition on leaves located on top one-third of the trees at the near side and far side of the target trees. Overall, deposition at treetops was improved by 9% when backstop was used. Since the backstop effectively blocks the scaping droplets, sprayers can be calibrated for more air and fine droplets to improve overall deposition with no drifting concern.
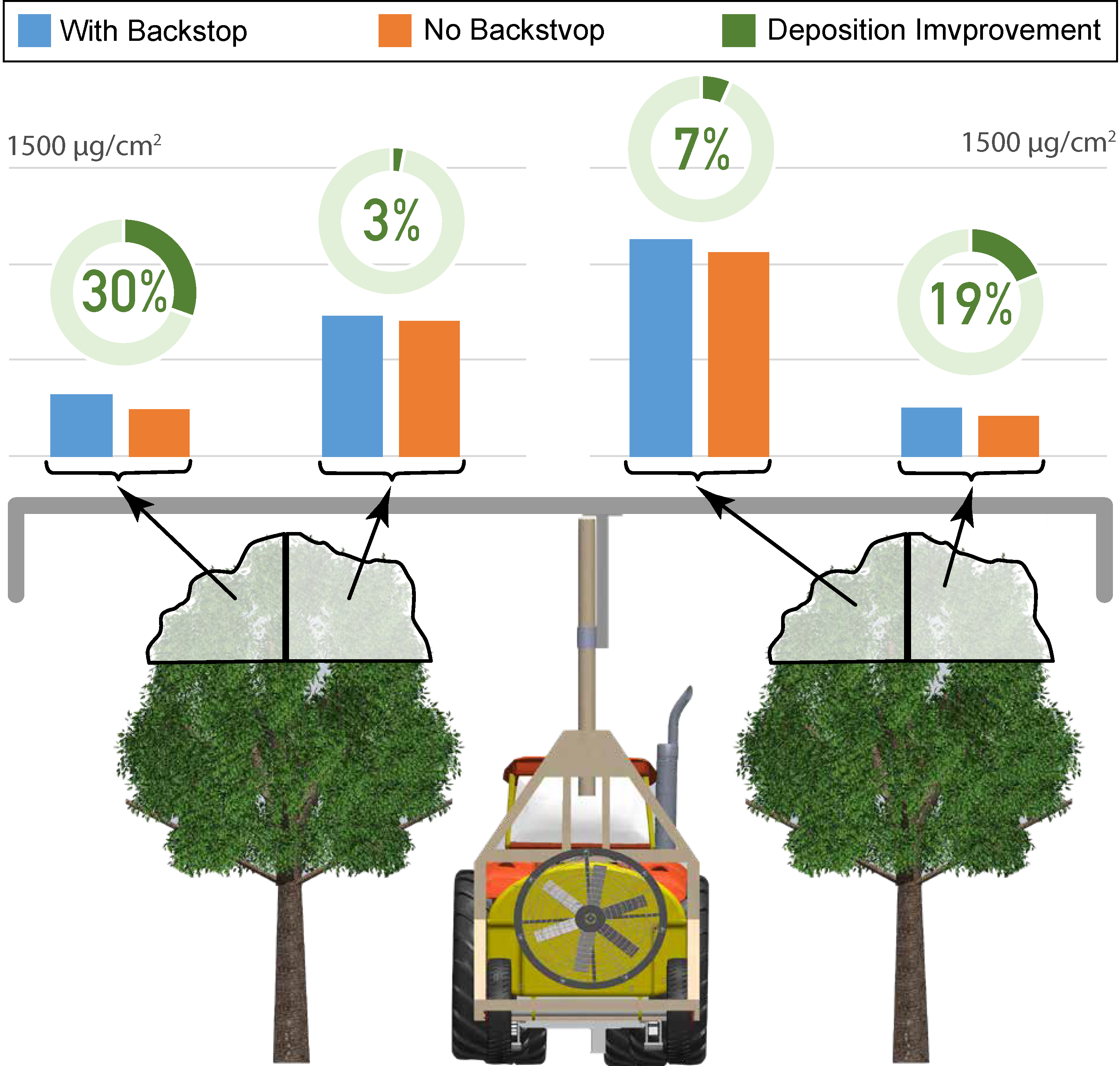
Conclusion
This project's main goal is to develop a spray attachment system that improves the performance of air-assist sprayers in Almond, primarily by reducing spray drift. The Spray Backstop system prototype developed in this project successfully blocked the spray cloud that passes the treetops and prevents them from escaping the orchard and becoming drift. Using the Spray Backstop system will allow growers to continue to adjust sprayers with more air and fine droplets that improve spray coverage in the hard-to-reach upper canopy area while helping manage drift.